Product Store
As businesses collaborate, the need for the separation of stores virtually or physically increases. The product store enables the cataloguing and pricing of products and offers that may or may not be produced by the company. This store is also enabled for multi-channel sales. This means that sales can be driven from your product store and finished goods store at the same time.
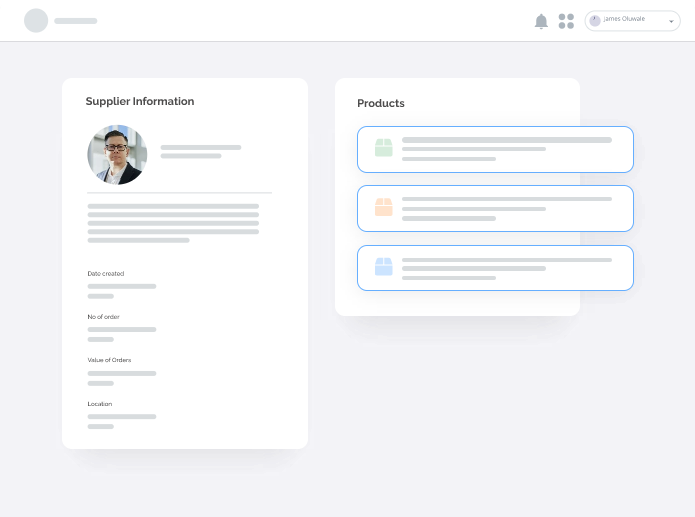
Inventory Accounting
When items are received to the warehouse, they are received with purchase prices recorded. Inventory accounting is driven by the issuance setup per warehouse. Issuance setting may be configured for First In First Out (FIFO), Last In First Out (LIFO), First Expiry First Out (FEFO) or may not be set at all. Each of these issuance setting may provide a different value in inventory accounting. Where the issuance setting is not configured, the inventory accounting will be based on Weighted Average Cost (WAC).
FIFO, LIFO, FEFO
The flexibility of being able to issue inventory on the basis of when they were received or when they will expire optimizes profitability. The need for returns, wastage and clearance discounts are drastically reduced. The feature is currently provided on the Inventory Management System for warehouse issuance and is not available on the Product Store
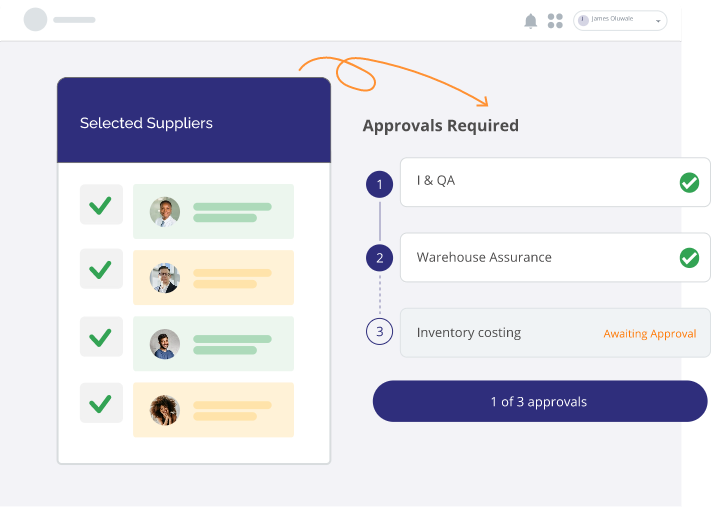
Stock-taking & Adjustments
Initial Migration of Stock balances has been made easy with the stocktake tool. Performing Stocktake periodically is an important part of maintaining accurate stock reporting. Where variances in stock levels are discovered after the stock taking exercise, a stock adjustment follows to correct all discrepancies. An analysis of stock taking reports over a specified period will be helpful in exposing issues of fraud or quality of products supplied.
Inspection & Quality Assurance
Prompt notification to users when there has been a significant change in level of inventory based on set Minimum Order and Restock level ensures that the business is made aware of the time to replenish stock.
Stock Level Alerts
Prompt notification of users when there has been a significant change in level of inventory based on set Minimum Order and Restock point ensures that the business is made aware of the time to replenish stock levels.
Expiry Management
There could be revenue loss from improper handling of products that are expired or about to expire . To avoid this, you can set up the frequency of Expiry Alerts to users that are to be notified when products are close to expiry. This will influence marketing and sales campaigns to rid the warehouse of these products. The First Expired-First Out issuance method can also be enabled to ensure that products with the closest expiry dates are issued out first.
Batch Generation & Tracking
Batch Number tracking allows you to track a batch of products from its creation right through to its sales. It enables continuous monitoring of raw materials throughout the process. As you receive a material, you can record its batch number. The batch of materials can then be tracked throughout the production process. Batch Numbers can be customized and generated based on the pattern of your business.
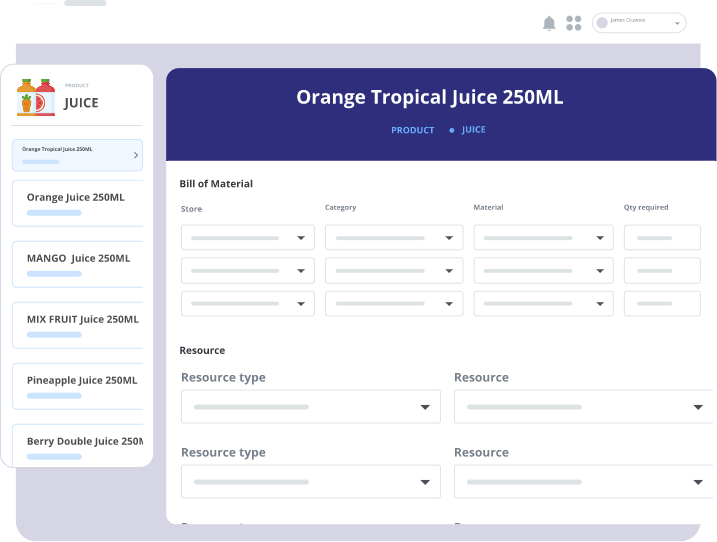
Bill of Materials
Bill of Materials provide accurate description of the materials and quantities required to produce the end product. This feature further enables the Manufacturer to know the true cost of production and enforces standardization in the product quality.